Just how to Recognize What is Porosity in Welding and Improve Your Strategy
Wiki Article
Recognizing Porosity in Welding: Checking Out Reasons, Results, and Avoidance Techniques
As experts in the welding industry are well conscious, recognizing the reasons, effects, and prevention methods related to porosity is vital for accomplishing robust and reputable welds. By diving into the origin causes of porosity, analyzing its harmful results on weld quality, and discovering efficient prevention strategies, welders can enhance their knowledge and abilities to produce top quality welds continually.Common Reasons For Porosity
Contamination, in the form of dust, oil, or rust on the welding surface area, develops gas pockets when heated, leading to porosity in the weld. Improper protecting occurs when the shielding gas, generally used in processes like MIG and TIG welding, is unable to totally safeguard the liquified weld swimming pool from responding with the bordering air, resulting in gas entrapment and succeeding porosity. Additionally, poor gas insurance coverage, usually due to incorrect flow prices or nozzle positioning, can leave parts of the weld unguarded, permitting porosity to form.Effects on Weld High Quality
The visibility of porosity in a weld can significantly compromise the overall top quality and honesty of the bonded joint. Porosity within a weld creates gaps or dental caries that deteriorate the structure, making it extra susceptible to fracturing, corrosion, and mechanical failing.Moreover, porosity can impede the effectiveness of non-destructive screening (NDT) methods, making it challenging to spot other issues or discontinuities within the weld. This can bring about considerable safety concerns, especially in critical applications where the structural stability of the welded parts is vital.
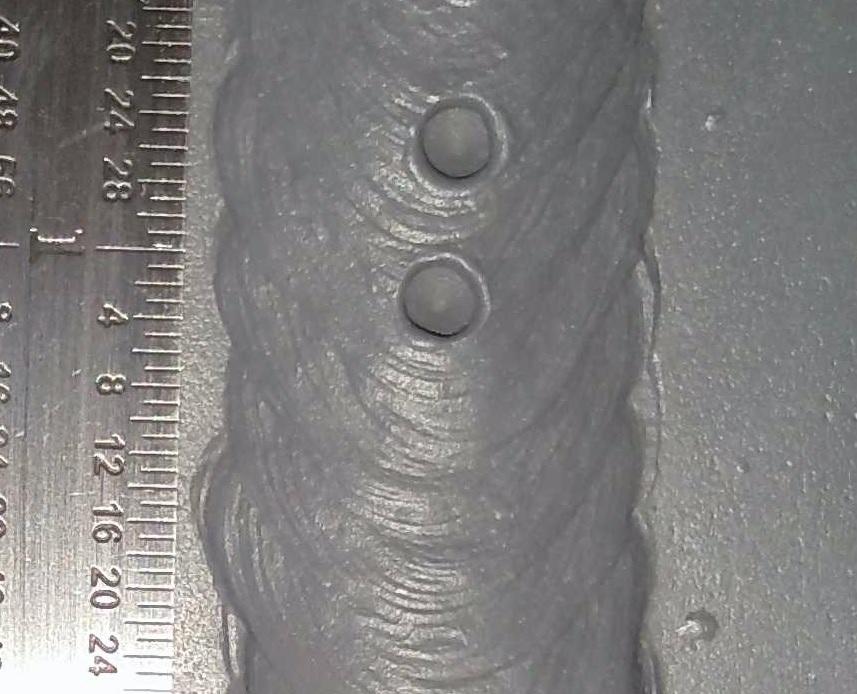
Prevention Techniques Introduction
Given the destructive effect of porosity on weld quality, reliable avoidance methods are critical to keeping the structural honesty of welded joints. In addition, picking the proper welding criteria, such as voltage, present, and travel rate, can assist reduce the danger of porosity formation. By integrating these prevention techniques into welding practices, the event of porosity can be dramatically lowered, leading to more powerful and a lot more dependable bonded joints.Value of Proper Shielding
Appropriate securing in welding plays an essential duty in stopping climatic contamination and making certain the stability of welded joints. Shielding gases, such as argon, helium, or a combination of both, are frequently made this hyperlink use of to safeguard the weld swimming pool from reacting with components airborne like oxygen and nitrogen. When these reactive elements enter into call with the hot weld pool, they can cause porosity, resulting in weak welds with reduced mechanical homes.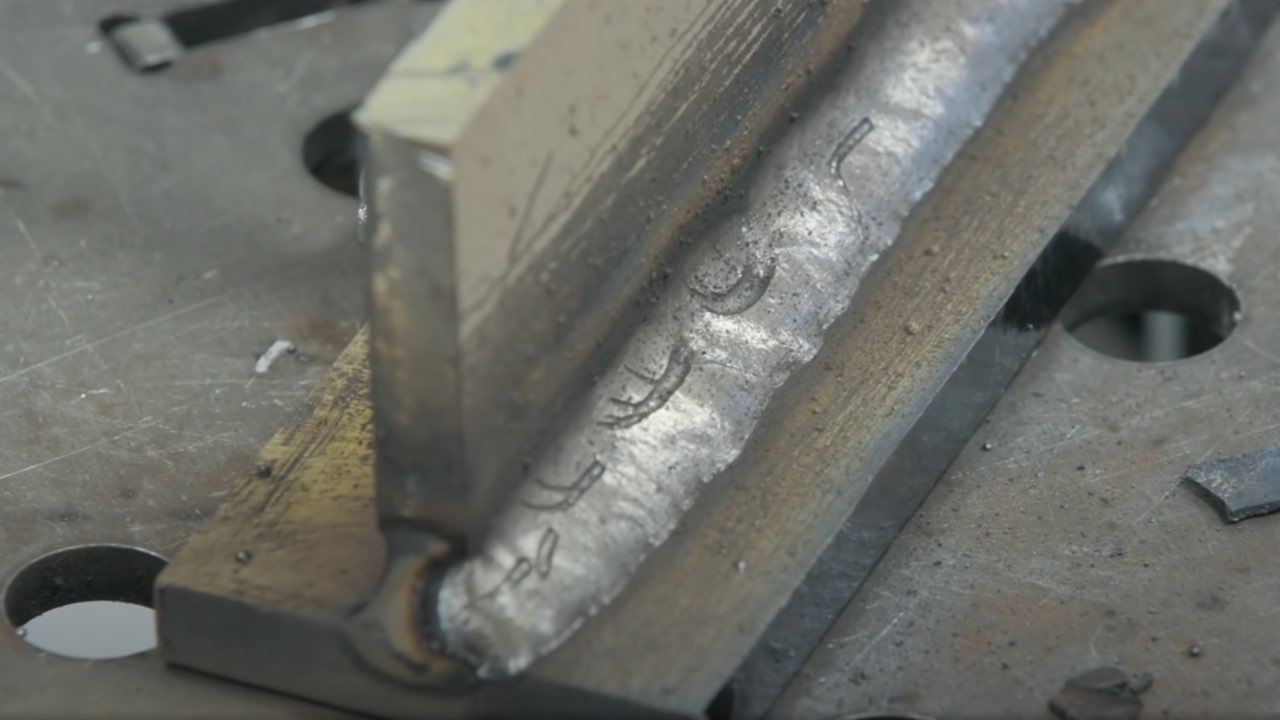
Insufficient securing can result in numerous problems like porosity, spatter, and oxidation, endangering the structural stability of the welded joint. For that reason, adhering to correct securing techniques is necessary hop over to these guys to produce top quality welds with marginal defects and ensure the longevity and dependability of the bonded parts (What is Porosity).
Surveillance and Control Techniques
How can welders properly check and regulate the welding process to make certain optimal results and protect against defects like porosity? By constantly monitoring these variables, welders can identify deviations from the perfect problems and make immediate changes to avoid porosity formation.
Furthermore, implementing appropriate training programs for welders is essential for checking and regulating why not try this out the welding procedure efficiently. What is Porosity. Informing welders on the significance of preserving consistent specifications, such as appropriate gas securing and travel rate, can help protect against porosity issues. Regular assessments and qualifications can likewise make certain that welders are proficient in monitoring and managing welding processes
Moreover, using automated welding systems can boost tracking and control capabilities. These systems can exactly manage welding specifications, lowering the possibility of human error and making certain regular weld high quality. By incorporating sophisticated surveillance innovations, training programs, and automated systems, welders can properly keep an eye on and regulate the welding process to lessen porosity defects and accomplish high-grade welds.
Verdict

Report this wiki page